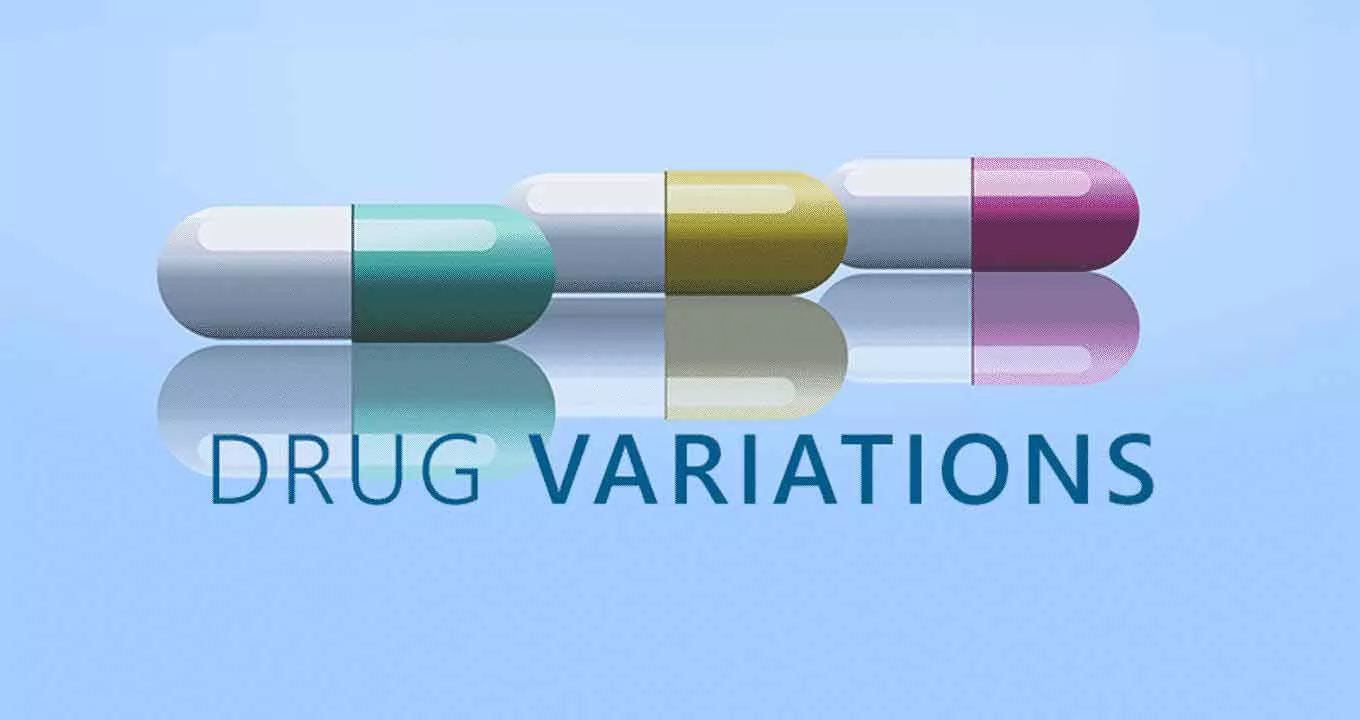
13 october 2021
From the moment a product receives marketing approval to the time it is withdrawn from the market, life sciences companies are required to manage and submit countless variations. This is the term used to refer to any change to the authorized product, regardless of how minor or major that change may be.
When companies receive marketing approval for their products, they must adhere to certain procedures, terms, and conditions, including the requirement to submit variations for any change to the product within a specified time period.
The “what” and “when” behind variations
The regulations surrounding variations in the European Union are well-established and the European Medicines Agency has taken steps to clarify and simplify the process for marketing authorization holders (MAHs). The European Commision’s 2012 amendments to the regulation for variations sets out which documents should be submitted for the different kinds of variations, the timing for submission of variations, and rules and recommendations governing groupings of variations.
Guidelines for submitting a variation also include information about the documents companies must submit, depending on the type of variation, and any conditions that may affect the marketing authorization. For example, a marketing authorization may be granted with a condition to make certain changes, conduct further studies, or provide clearer, more relevant data to support the submission. These conditions will need to be met within a certain timeframe and if companies don’t comply with this commitment in the agreed time, their product authorization could be suspended or withdrawn.
Furthermore, the regulations change fairly frequently and even products released years ago must comply with new requirements. As an example, MAHs must now identify in the product information which excipients of any authorized product can have a known effect (to be declared in the labelling and leaflet) and this updated information is done as a variation. Also, to ensure they are aligned with good manufacturing practice, any required changes to manufacturing processes must be handled through a variation. An example is the requirement to address nitrosamine impurities and show that any risks are managed and minimized and to demonstrate that the company is monitoring any risk that may be posed to the patient.
MAHs also are required to submit a variation if there are any updates to manufacturing methods, if there are changes to any pharmacopeial monograph, and, most crucially, if there is any change that may be relevant to safety assessments, such as change of composition, mode of use, or dosage or any recently observed adverse events or change in the frequency of adverse reactions.
A clear process
The regulations behind variations are just one element in managing the process. It is also important that companies know how to approach these changes. Documentation needs to be clear and consistent and the information included should not be so complicated that it will slow down the review process. Determine your strategy. Should you combine changes in a grouping of variations or submit several minor variations? Is your approach logical? Have you followed the required timelines?
Variations are now submitted electronically and the health authorities have simplified the process with clear guidelines and classifications making it easier for companies to select the right type of variation, the documentation that needs to be included, and other changes that might be triggered by the variation. For example, a change in manufacturing composition will trigger changes in the product information, artwork, and other areas, and that information needs to be included in the support documentation.
Knowing the right processes and variations is key to safeguarding products on the market. For example, with Type 1A variations, the MAH submits a notification to all relevant authorities within a year of implementing the variation. This means the MAH doesn’t need to wait for a response from the authorities, and the product can continue to be marketed without disruption. However, if a company delays their submission or if a grouped variation includes a major change, it must go through approval, which means nothing can be implemented until approval has been granted, and this can result in long delays, often affecting multiple markets and patients.
By carefully following the requirements and regulations, adhering to timelines, communicating with the authorities and having a clear strategy in place for managing variations, companies place less pressure on the competent authorities as well as on their own internal personnel. Furthermore, by staying ahead of the regulations and anticipating changes, companies can reduce the risk of running into problems with their marketing authorization.
Working with ProductLife Group
With an experienced regulatory affairs team in markets across Europe and globally, ProductLife Group can not only manage variations on behalf of clients, but can also advise you on the best strategy for managing a variation and working with the authorities. This includes the approach to follow, the type of documentation to include, and how long the process of preparation, submission, and approval will take.
Integral to supporting clients at a local and global level is staying up to date with the regulations – from larger developments to small, technical adjustments and changes to the form or forms that must be used for a variation submission. In addition, PLG’s regulatory team supports clients with regulatory intelligence that might affect other parts of the organization; for example, if a change could potentially affect pricing and reimbursement.
PLG’s strategic approach to supporting clients throughout the product lifecycle ensures that any variations and related actions are managed in a way that delivers the best outcome for the client and their marketed products.
Go to our Events to register
Go to our News to get insights